Shop System enables affordable batch production of high-quality metal parts on the shop floor starting at $150,000
FRANKFURT, Germany — (BUSINESS WIRE) — November 19, 2019 — Desktop Metal, the company committed to making 3D printing accessible to manufacturers and engineers, today announced the launch of Shop System™, the world’s first metal binder jetting system designed for machine shops and metal job shops. For the first time, shop owners can leverage affordable, high-quality binder jetting technology to print end-use metal parts with unparalleled speed, print quality, and productivity. The system was unveiled during Formnext 2019, a leading additive manufacturing conference, in Frankfurt, Germany.
This press release features multimedia. View the full release here: https://www.businesswire.com/news/home/20191119005056/en/
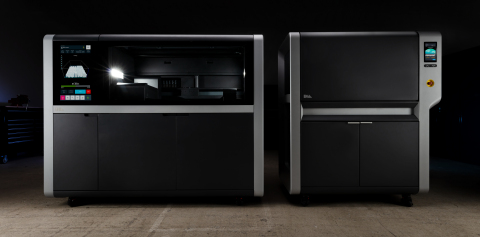
The Shop System™, the world’s first metal binder jetting system designed for machine shops and metal job shops, starting at $150,000. (Photo: Business Wire)
Offering the most cost-effective solution in the industry starting at $150,000, this high-speed, single-pass print engine introduces high-quality binder jetting to an entirely new market of machine shops and metal fabrication job shops, a nearly $180 billion global industry. With the Shop System, shop owners can eliminate many of the constraints previously seen with traditional manufacturing methods like CNC machining and tap into new opportunities to reduce their costs and increase revenue.
With the addition of this new system, Desktop Metal’s solutions portfolio covers the full metal product lifecycle - from the office-friendly Studio System™ for low volume prototyping, to the Production System™ for mass production, and now with the Shop System, mid-volume runs of complex metal parts on the shop floor.
“Since the launch of our metal 3D printing platforms, Studio System and Production System, Desktop Metal has changed the rules of traditional metal manufacturing solutions with innovative approaches that reduce costs and significantly increase speed and print quality for our customers,” said Ric Fulop, CEO and co-founder, Desktop Metal. “Our current technology has significantly disrupted low- and high-volume production in metal manufacturing, yet there was still a real need for a robust solution that also captures mid-volume production and enables affordable, reliable and flexible batch production of complex parts for machine shops. For the first time with the Shop System, machine shops will be able to make that a reality.”
Introducing the Shop System™
The Shop System platform’s end-to-end solution, including printer, powder station, and furnace, seamlessly integrates with existing shop operations. Users can print end-use metal parts that span a variety of industries, including manufacturing, tooling, automotive, consumer, electronics, and marine, with the quality, surface finish and tolerances needed to co-exist with machining - up to 10 times faster than laser powder bed fusion and at a fraction of the cost per part.
The Shop System is able to print a batch of complex parts every six to 12 hours, enabling tens up to hundreds of near-net-shape metal parts to be printed each day - as much as 70 kg of steel per day. Because parts on the Shop System print fully supported in their powder bed and feature hand-removable sintering setters, users will avoid hours of labor machining or wire EDM off support structures typical of laser-based systems. This in turn, reduces the total number of manufacturing steps needed, increasing shop productivity and capacity without requiring additional headcount or machinist hours.
With a spot size of 16 microns per drop, 1600 native single pass DPI and distributing up to 670 million drops per second, the Shop System is the highest resolution single pass binder jetting printing system on the market - delivering 33 percent higher resolution than comparable single pass binder jetting systems. Also offering the smallest droplet size for single pass binder jetting systems at approximately 1pL and automated drop multiplexing up to 6pL, the system allows for superior surface finish, bleed control and rich feature detail at high speed. The system’s 70,000 nozzles per line have built in five times redundancy - 25 percent higher than other single pass binder jetting systems - to help to avoid jet-outs resulting in enhanced quality and reliability for shop owners. A revolutionary recoating system delivers unprecedented powder bed uniformity for ultra high accuracy parts.
“Shop owners have been enamored by the versatility, speed and cost reduction that binder jetting technology can provide, but until now, it hasn’t been accessible to them,” said Jonah Myerberg, co-founder and CTO, Desktop Metal, who led the technical development of the system. “The Shop System offers users the same fully-dense metal parts at an affordable price that works in harmony with machining on the shop floor. What’s more, the system enables owners to both save and make money by eliminating tooling costs, lowering lead times, and bringing in new business because of an improved part-cost equation.”
“In our business, quality and response time are critical. The ability to simultaneously produce multiple complex parts with no custom setups is a productivity game changer,” said Bruce Ferguson, President and CEO of Hansford Parts & Products, a contract manufacturer of CNC machined parts for automotive, aerospace, medical, and electronics industries based in Macedon, NY. “We are looking to additive manufacturing to produce geometries unattainable with conventional machining, free up CNC capacity, and reduce part costs.”
“At Zyci, we are engineered for speed, with a culture that obsesses over exceeding customer expectations. With customers across aerospace, medical, electronics, robotics, luxury goods, and defense, we are a trusted partner for both high volume and low volume, high mix jobs,” said Mitch Free, CEO and founder of ZYCI CNC Machining. “The Shop System’s ability to seamlessly go from producing one-offs, to hundreds of parts per day, is an important breakthrough for CNC shops looking to both cut costs, and bring in more revenue.”
With variable configurations (4L, 8L, 12L and 16L), the Shop System is designed to scale to each shop’s throughput, including:
-
Mixed-volume production of various geometries
Production of various part geometries simultaneously without the need for multiple setups.
-
Production of low volume batches
Cost effective production of low volume batches of complex parts due to elimination of tooling.
-
Mid-volume production of hundreds of parts per day
Production of hundreds of near-net-shape parts every day with dramatically reduced labor costs and expanded geometric flexibility.
Shop System Availability
General availability for the Shop System is Fall 2020. Customers interested can purchase a system starting today. Pricing starts at $150,000 for the 4L (350 x 220 x 50mm) and scales to $225,000 for the 16L version (350 x 220 x 200mm). For more information on the Shop System, please visit https://www.desktopmetal.com/products/shop.
About Desktop Metal
Desktop Metal, Inc., based in Burlington, Massachusetts, is accelerating the transformation of manufacturing with end-to-end 3D printing solutions. Founded in 2015 by leaders in advanced manufacturing, metallurgy, and robotics, the company is addressing the unmet challenges of speed, cost, and quality to make 3D printing an essential tool for engineers and manufacturers around the world. Desktop Metal was selected as one of the world’s 30 most promising Technology Pioneers by the World Economic Forum; named to MIT Technology Review’s list of 50 Smartest Companies; and recognized among the most important innovations in engineering in Popular Science’s “Best of What’s New.” For more information, visit www.desktopmetal.com.
View source version on businesswire.com: https://www.businesswire.com/news/home/20191119005056/en/
Contact:
Desktop Metal, Inc.
Lynda McKinney, 978-224-1282
Head of Communications
Email Contact